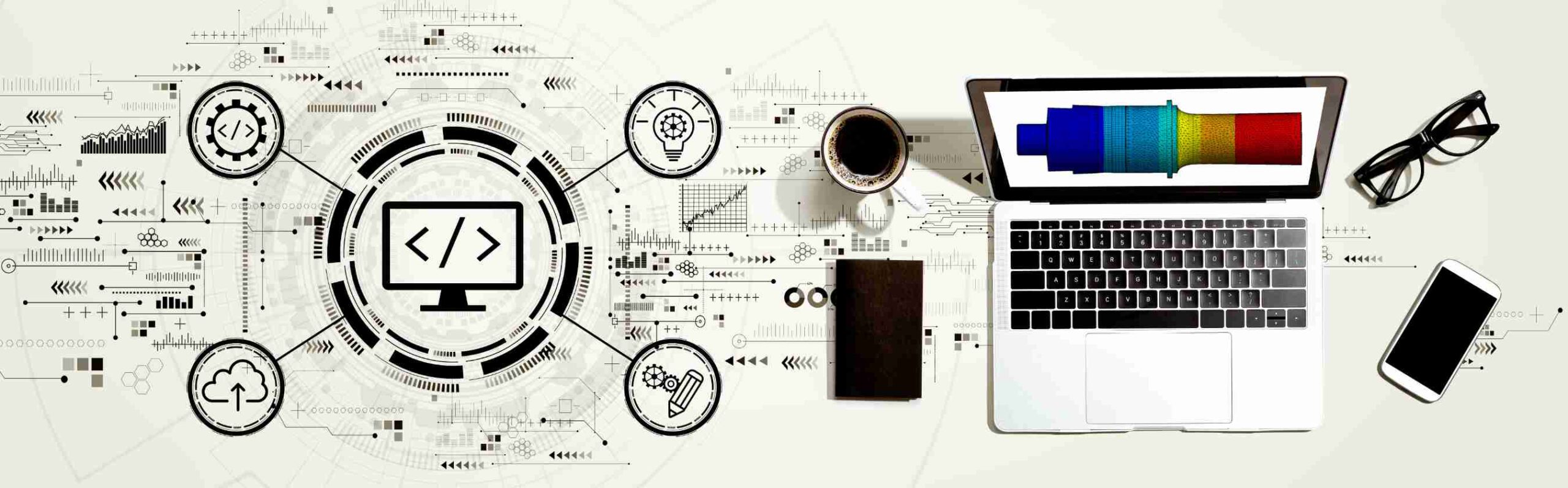
Simulation & Measurement
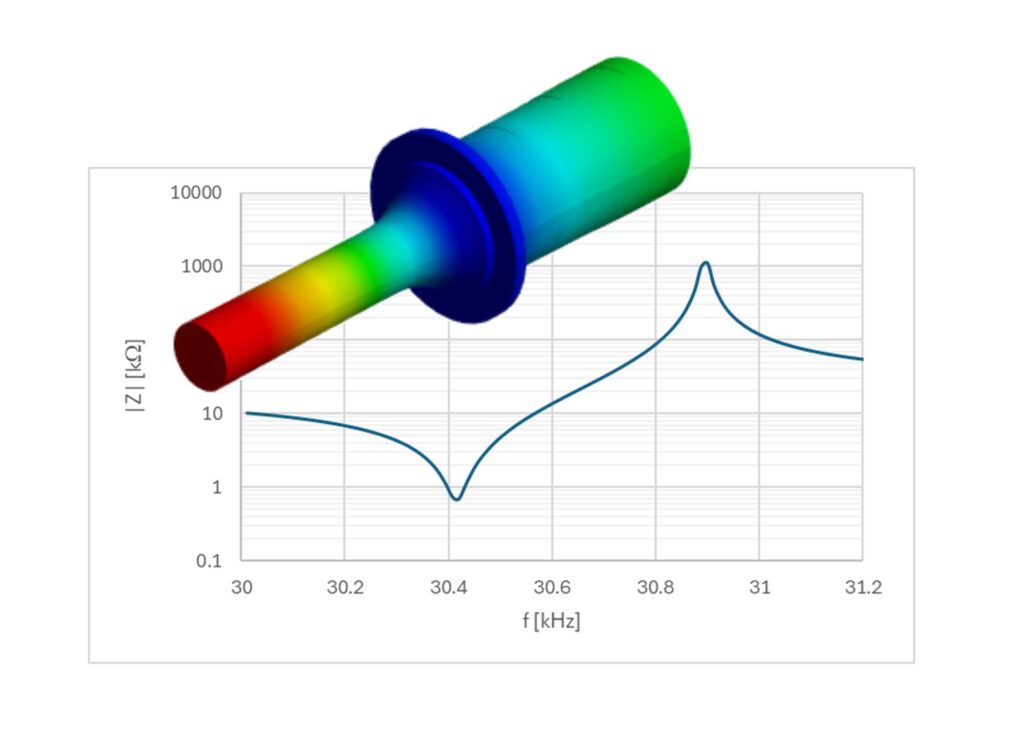
Modelling and simulation of piezoelectric systems
Beside analytical calculations and simplified numerical models, we use the finite element method (FEM) for the frequency-accurate design of ultrasonic resonators. In the modeling, we are able to represent very precisely:
- the „active“ piezoelectric material behavior (dielectricity, piezoelectricity, mass and compliance)
- the directional dependence of the material properties (anisotropy)
- the change of polarization direction in stack actuators
- material-specific damping properties
- the resonance characteristics of piezoelectric transducers
- piezoelectric actuators and sensors
Laser measurement of ultrasonic vibrations
Using our laser measurement technology, we are able to analyse dynamic processes with high precision and contactless, without affecting the sensitive behaviour of the sensors, actuators, or ultrasonic transducers. The use of this special measurement technology allows for example:
- the highly accurate visualisation of vibration distributions in the µm amplitude range
- the error analysis in our customers’ products (e.g. spurious resonances)
- the analysis of tolerance-related frequency and amplitude variations in production
- the validation of results of electromechanical simulations (FEM) by measurements
- the optimization of sensitive structural oscillators
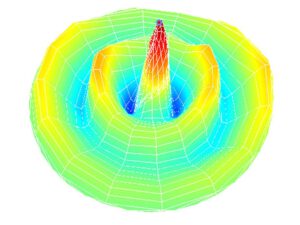
Application tests and construction of test benches
After simulating ultrasound systems, comprehensive and in-depth experimental analysis of the systems is of crucial importance in the development process in order to validate model results and to be able to investigate influences that are difficult to represent in the model. To test new ultrasound processes or to test ultrasound converters, sonotrodes and tools, we can rely on extensive measurement equipment as well as many years of experience and creativity in setting up measurement environments. In this context, we can offer the following services, among others:
- Short-term implementation of application tests for various ultrasound processes with existing ultrasound systems (various frequencies and power classes)
- Comprehensive characterisation of processes by a variety of measurement methods (laser measurement, precise temperature measurement, simultaneous measurement of electrical and mechanical quantities, process-accompanying measurements)
- Development and construction of suitable test benches for testing ultrasonic systems (e.g. defined loads, applications in water,…)
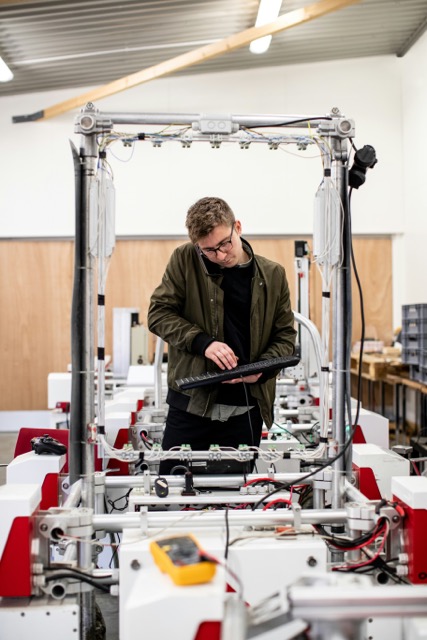
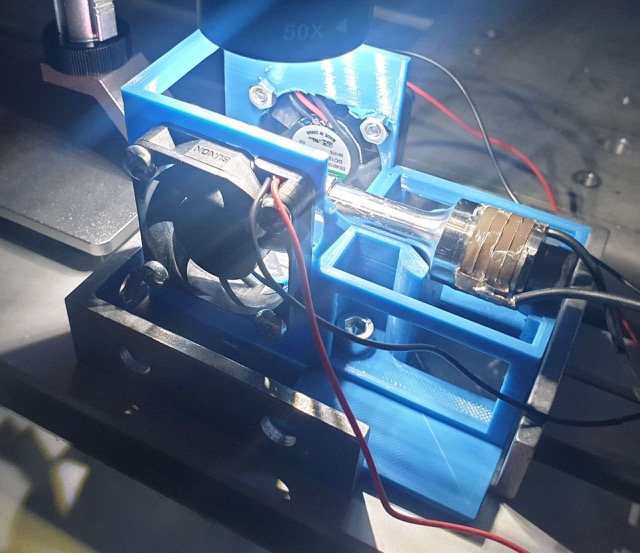
Material fatigue tests (ultrasonic Wöhler curves)
To record Wöhler curves, measurements with load cycle numbers in the three-digit million range are necessary. By using ultrasonic frequencies, high cycle numbers can be achieved within an hour, which would otherwise require weeks of testing. With existing ultrasonic actuators, our know-how for dimensioning suitable ultrasonic samples and our ATHENA ultrasonic generator, we have the perfect test environment to test your materials for fatigue strength.
Sound simulation, ultrasonic acoustics and cavitation measurement
There is always an interaction between the ultrasonic transducer and the sound field it generates. In particular, in processes involving liquids, the adjacent fluid influences the characteristics of the ultrasonic transducer. In other applications, the nature of the sound field generated is crucial for the application (distance sensors) and should be influenced by design measures.
We use the finite element method (FEM) to calculate sound fields in the ultrasonic range and their interaction with the sound generator. We also have measurement methods for the experimental analysis of ultrasonic acoustics, even in cavitations-based processes.
- FEM simulation of sound fields and their interaction with the ultrasonic transducer (fluid-structure interaction)
- Sound measurements in air and liquids in the ultrasonic range (ultrasonic microphone and hydrophone)
- Experimental analysis of cavitation activity (acoustic measurements, foil tests, sonoluminescence, cavitation noise)
- Analysis of damping effects (e.g. due to non-reflective edges, due to fluid viscosity or due to cavitation)
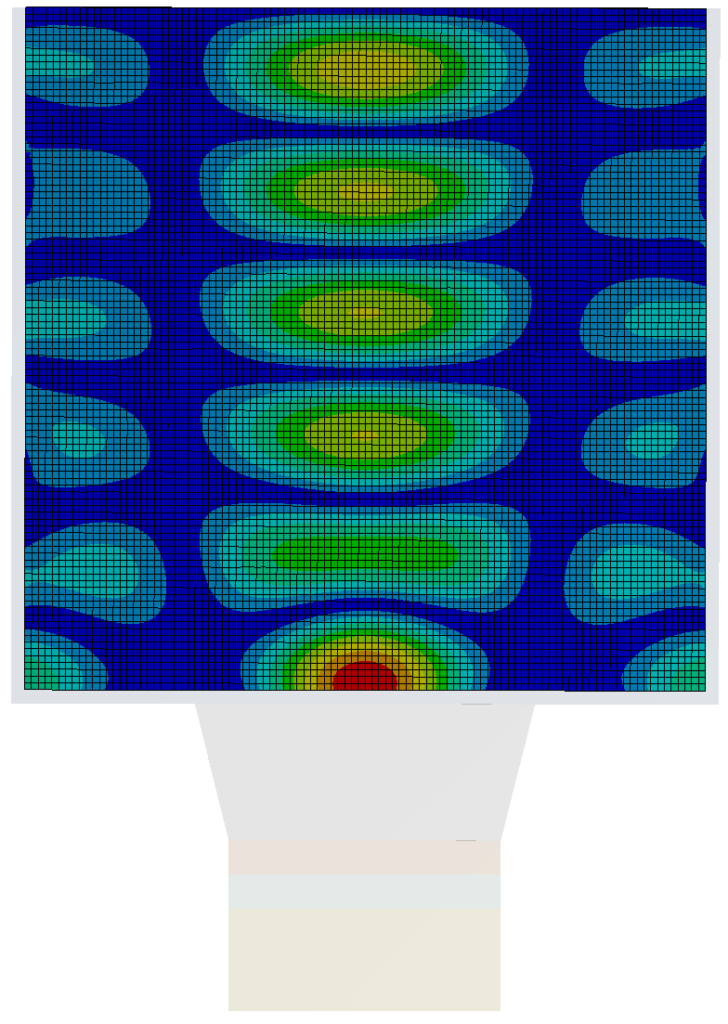
Your contact:
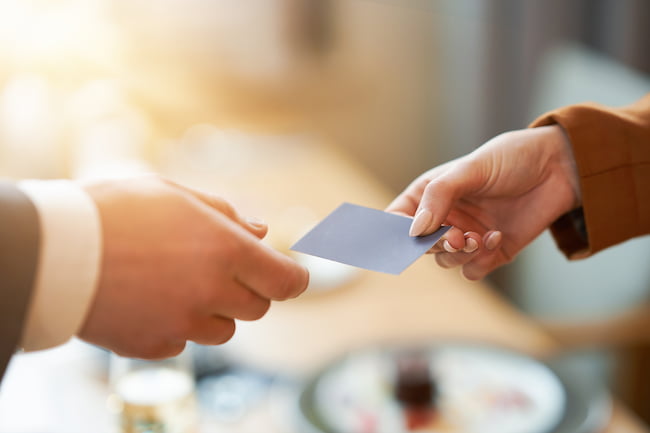